In wire harness assembly, the decision to braid wires isn’t just aesthetic—it has real, functional advantages. Whether you’re designing for high-vibration environments or looking to improve electromagnetic interference (EMI) shielding, braided harnesses can make a measurable difference.
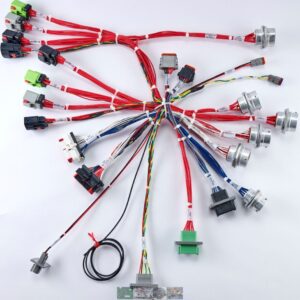
Three reasons why we braid our wire harnesses (and why it might be the right choice for your next project):
1. Protection from Vibration and Temperature
In many industrial and automotive applications, vibration is constant—and a common cause of wire fatigue and failure. Additionally, some parts of the harness may be located near other parts that operate at very high temperatures or have sharp edges. Braiding helps absorb that motion and keeps wires more stable, extending the life of the harness even in harsh environments.
Industries where vibration is a significant concern include:
- Heavy Machinery: Heavy machinery in manufacturing plants often operates under conditions that produce significant vibration, impacting the longevity of wire harnesses.
- Rail and Transportation: Trains and other rail vehicles experience continuous motion and vibration, requiring durable wire harness solutions.
- Heavy Equipment: Agricultural equipment, construction equipment such as cement mixers, and other heavy equipment often have parts that vibrate or have fluctuating temperatures that mean wire harnesses must withstand a range of environments.
- Automotive: Vehicles, especially those operating on rough terrains, subject wire harnesses to constant movement and vibration.
- Aerospace: Aircraft systems experience continuous vibration during flight, necessitating wire harnesses that can withstand such conditions.
While specific quantitative data on the strength improvement provided by braiding may vary, it’s well known that braided wire harnesses offer enhanced durability and resistance to mechanical stress compared to non-braided wire harnesses.
2. EMI Shielding
Electromagnetic interference (EMI) can compromise signal quality in electrical systems—leading to data loss, communication glitches, and equipment malfunction. Braided coverings add an extra layer of defense, reducing EMI and helping maintain signal integrity.
This type of shielding is especially critical in data-sensitive or high-noise environments, where even minor interference can cause major problems.
Industries where EMI shielding is essential:
- Medical Devices: Accurate data transmission is critical for monitors, imaging equipment, and diagnostics. EMI interference isn’t just inconvenient—it can affect patient safety.
- Aerospace and Defense: Aircraft, satellites, and communication systems demand uninterrupted signal transmission. EMI shielding is required by most military-grade wiring standards.
- Telecommunications: Data cabling, networking hardware, and signal processing systems rely on clean signal paths to function reliably.
- Automotive Electronics: Modern vehicles use CAN bus systems, infotainment, radar, and ADAS—all of which require protection from electrical “noise.”
- Industrial Automation: Factories packed with motors, drives, and sensors create a noisy EMI environment. Shielding keeps control systems stable.
Fun fact: Braided shields can reduce EMI by 60–90%, depending on the density and material of the braid.
3. Clean, Organized Builds
Braiding doesn’t just protect—it brings order. A braided wire harness looks cleaner and more professional, which can make a real difference during installation, inspection, and service.
A well-braided harness is:
- Easier to route through tight spaces
- Less likely to snag, twist, or tangle during assembly
- More resistant to unintended strain during movement or repositioning
- Easier to identify and trace individual circuits, especially when color coding is used underneath the braid
This is particularly valuable in industries where maintenance access is tight or critical, such as:
- Medical Equipment: where a clean, well-organized harness reflects attention to detail and simplifies service calls
- Control Panels and Enclosures: where clean routing supports heat management and future upgrades
Bonus: Some customers perceive braided harnesses as higher quality—even before the product is powered on. The visual neatness reinforces your reputation for precision and reliability.
In short, braiding supports not just performance, but perception—and that matters, especially when your harness is the first thing someone sees when they open a panel or pop a hood.